Blog
Maximizing aircraft fuel efficiency: Don’t skimp on R&D
Part 4 in a series featuring interviews with experts who worked with the ICCT on our cost assessment of near- and mid-term technologies to improve new aircraft fuel efficiency. The aim of the series is to highlight the potential fuel efficiency improvements of “clean-sheet” aircraft designs, to give a sense of how they influence the fuel efficiency trends in general, the risks that come with them, and, most importantly, what might be done to encourage them.
Many technologies found on a commercial aircraft today started as NASA Aeronautics’ research projects. We sat down with Dr. Fay Collier, Associate Director for Flight Strategy, Integrated Aviation Systems Program at NASA Aeronautics. Dr. Collier just completed a six-year tour at NASA Environmentally Responsible Aviation (ERA) as Project Manager, developing technologies that cut aircraft noise, emission, and fuel use. We spoke to him about NASA’s contribution to technologies already in use on aircraft flying now, the ERA project, and a new NASA initiative to demonstrate these environmentally responsible aviation technologies. He also shared his view of what he thinks a typical aircraft in 2050 would be like, and what it will take to make that future a reality. A transcript of our conversation, edited for length and clarity, follows.
ICCT: Thank you for joining us today, Fay. Before we get to the exciting technologies of the future, I’d like to talk about the past. Historically, how much of the technology developed by NASA found its way to a commercial aircraft?
Fay Collier (FC): I don’t have any specifics in terms of numbers, but over a 50-year period we’ve had quite a bit of technology that has evolved from computational fluid dynamics, through wind-tunnel testing, found its way to a demonstrator airplane, and then eventually ended up on a commercial airplane. I can give you an example that I was involved in 20 to 25 years ago that took that same path, and it’s a technology known as laminar flow. While laminar flow wings are still a frontier, we have laminar flow on the Boeing 787 nacelles as well as one of the tail surfaces.
ICCT: What lessons have you learned from these success stories?
FC: One of the lessons learned is the most successful technologies find their way on to an airplane through strong partnerships with the OEMs: the engine manufacturers and aircraft manufacturers themselves. And as we mature the technologies from the Technology Readiness Level, or TRL-1, which is lab-based, all the way to certification, which is TRL-9, the earlier we can attract a partner from the industry the more likely that the technology will find its way on to a commercial product. So we try to get our industry partners involved early through, in some cases, contractual work because the risk is so high, they are not ready to invest their own dollars. But eventually, once the technology becomes known we can get more collaborative work going where they’re co-investing in a public-private partnership.
The other piece of that is making sure that we’re addressing practical issues associated with putting the technology on aircraft. Things like maintainability over time—trying to eliminate any aspect of the technology that may require increased service or maintenance to the airplane. These “ilities” are very important, as well as making sure we’re working with the certification authorities as early as possible to look at certifiability of the technology. Those are ways to accelerate the application to commercial aircraft and to benefit the flying public.
ICCT: In the ERA Report we saw that the demonstrated technologies could “cut airline fuel use in half.” Can you comment?
FC: We had a suite of technologies—engine and air frame related—that were needed to meet these targets. We were working on engine technologies with General Electric, Pratt & Whitney, and Rolls Royce. And on airframe technology we were working with Boeing and Gulfstream and a number of other entities to mature technologies like, for example, weight reduction and drag reduction. Those are the major components on the airframe side that we focus on. And that 50% number is a rolled-up engine plus airframe contribution compared to an aircraft that we know quite well. Our reference was Boeing 777-GE90 combination and NASA’s internal model was calibrated to represent that airplane. We were able to run a technology through this overriding system modeling capability and this analysis, along with risk assessments, helped us downselect the technology portfolio that we wanted to mature in ERA. [The model] didn’t make the decision for us, but helped guide our decisions so that the technologies we picked would have this impact.
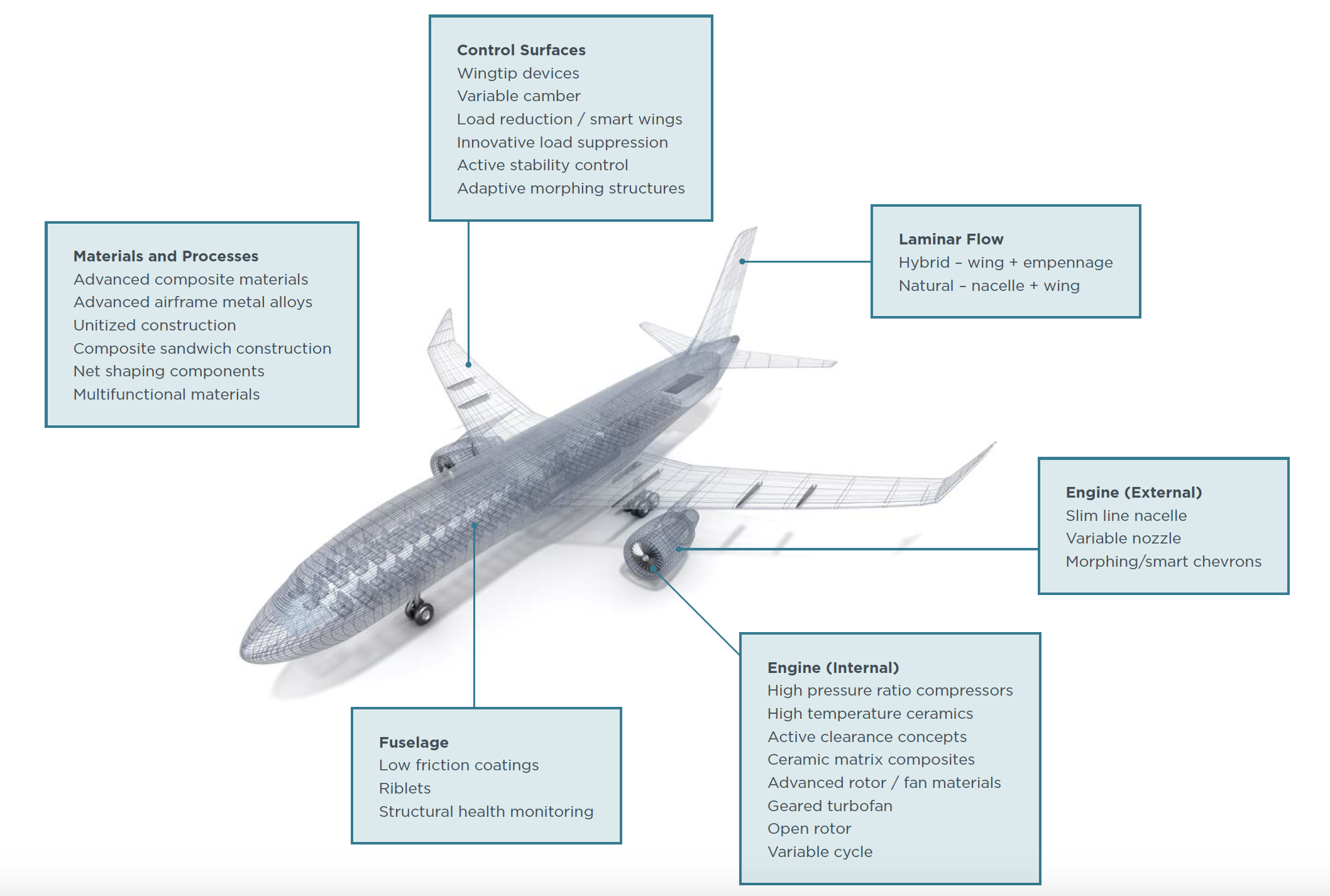
Figure 1. One of the technologies developed under NASA ERA is Active Flow Control enhanced vertical tail (left), flight tested on the NASA/Boeing B757 ecoDemonstrator (right). [Source: Pictures courtesy of Dr. Fay Collier]
ICCT: Do you have any comment on what you think is going to be realized in the “real world”? Are we going to actually see these large improvements in the future?
FC: Well, the first thing that the public needs to know is that over the last 50 years prior to ERA tremendous progress was made to reduce fuel consumption from air travel. To continue that trend, that actually comes out to about 1.5% per year, you might imagine after that amount time we’re maybe getting close to an asymptote. But there is a little bit of room for improvement left in the tube-and-wing design. NASA had established a midterm goal of 50% reduction in mission fuel burn—that is, fuel burn from take-off to landing—that might take a configuration change to actually achieve. That was actually part of the theory or hypothesis that we started ERA with: that the goal will be difficult to achieve using conventional tube and wing technology that we all fly around in today.
ICCT: Why aren’t we yet seeing any advanced configurations on the horizon?
FC: Well, we’ve been working on maturing the technology required to enable that type of configuration along with a few others, actually. The answer to your question is really about risk reduction and the appetite for risk that the industry has. As we go from TRL 1, which is lab based, through certification we buy down risk and as we’re buying down risk, these concepts / technologies become more attractive to the industry. When you go for a complete configuration change like tube and wing to blended or hybrid wing body, or the double bubble type configuration, that takes a whole lot more work—you got to be concerned about how it fits into the infrastructure, and how it’s perceived by the flying public.
The risk associated with the investment of such a major change is large, but we have a history over the previous hundred years of aviation of taking these risks and opening up these new S-curves. Fifty years ago, we had such a change with the advent of the jet age and the swept wing and the industry might be ready to begin over the next 10 to 20 years to consider that next new S-curve that might be represented by some of these advanced configurations. So it’s not an overnight or immediate change. These are changes that evolve over time and they’re also market driven, so the market must be demanding the advanced capabilities that these configurations represent in order to make these leapfrog-type advances.
ICCT: The S-curve for the jet age is an example of when new technology had clear benefits for the airlines and consumers in terms of speed, range, and safety. What would the direct benefits be for airlines and the flying public from the upcoming S-curve?
FC: Conventional tube and wing passenger jets have improved tremendously since their advent. Alternate configurations under study by NASA will likely be MUCH quieter, possibly reducing community noise by half to one quarter of current levels around airports. Because the emerging alternate configurations are highly integrated, and may include advanced hybrid electric propulsion systems, the carbon footprint of aviation will possibly be simultaneously reduced by an additional 50 percent.
ICCT: You mentioned that this change is market driven. Do you think that the market demand for these advanced configurations could be generated or accelerated by some sort of government policies? If so, what could they be?
FC: Acceleration. The government’s R&D role is to mature technology that works toward established technical challenges, technology that needs maturing to become attractive to OEMs. Airport noise remains the number one impediment to growing the US air transportation system. The cost of fuel burned remains a significant fraction of direct operating cost for airlines. To remain viable, airlines will look toward the government and suppliers to mature and implement technology to address these operational challenges.
ICCT: Is there anything else that the government can do in order to push these technologies to be adopted by OEMs?
FC: We’ve been talking about the government’s investment in technology, and we have a long history of doing research and handing research off to the industrial base to evolve or improve the capability. And I think all the improvements that occurred in the last 50 years in noise and mission fuel burn really were a direct result of government investment.
There’s a second way the government plays a role and that’s from regulations, for example on community noise. The government takes an advance in technology and enforces a regulation that essentially an aircraft can make no more than a certain amount of noise at a given time of day. That’s the second way the government can stimulate investment.
ICCT: Let’s talk about New Aviation Horizon.
FC: It’s an initiative we’ve been advocating for several years now. We are proposing it to be centered around X-planes—experimental airplanes. NASA has a long history of flying experimental X-planes, using them to create major breakthroughs for aviation. And New Aviation Horizon is using the spirit of the X-planes as we know it to continue creating major breakthroughs for aviation. One that we’re focused on right now is on supersonics—reducing or eliminating the sonic boom associated with supersonics over land flights.
NASA is also preparing a series of subsonic X-planes where we can demonstrate some of the advanced configurations we matured in ERA and in other NASA work. We have one in operation right now, the X-57, called the Maxwell. The X-57 is focused on hybrid electric technology. Essentially, greater electrification of aircraft could reduce the overall carbon footprint of flying. This is a first step towards electrification, which has a long roadmap associated with it, but progress is being made rapidly. There is a series of other subsonic X-planes that we are planning, with the design and development of the first one beginning in 2020. [Two of these concepts are pictured here in Figure 2.]
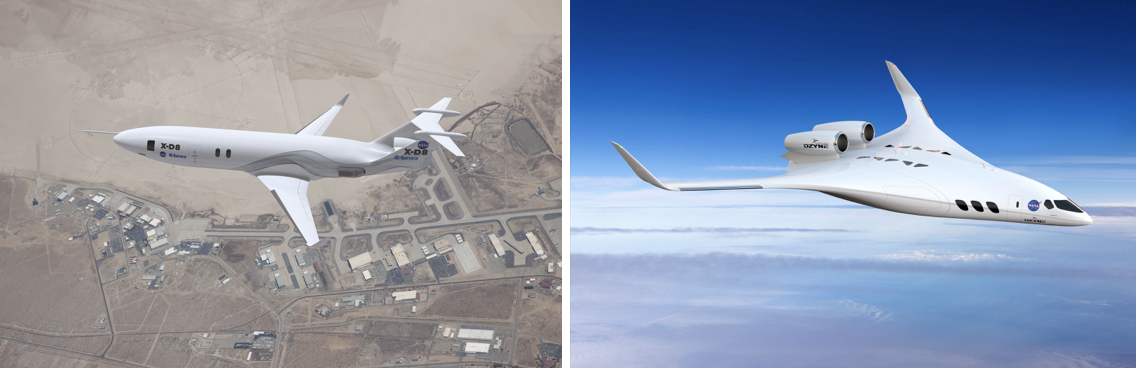
Figure 2. Aurora D8 integrated double-bubble (Left) and DZYNE Regional Jet-sized Blended Wing Body (Right) X-plane concepts. [Source: Pictures courtesy of Dr. Fay Collier]
ICCT: With the X-planes in mind, describe the state-of-the-art commercial airplane in 2050.
FC: In 2050, based on the work that we have done to date, the aircraft itself more than likely will be much more . . . I’ll use the word “integrated.” Right now, the way the aircraft looks is, we have a tube—imagine the description of where the passengers are seated as a tube, we have wings attached to the tube, and then we have engines attached to the wings. In the future, we’ll see highly integrated fuselages, wings, and engines, and you may not even be able to discern, by looking at it, where the engine is. The overall integration of the wing, fuselage, and engine nacelles can improve the drag profile associated with the airplane and by itself, just the change in configuration, can result in a 10% to 15% reduction in fuel burn, so it’s a huge potential there. A lot of work that we’ve been doing is trying to prove out that potential, and these X-planes would be aimed at demonstrating the potential of these concepts—not just one technology but a combination of numerous technologies. These are opportunities that take a long time to figure out, and that’s why we’re talking why the X-planes are needed to reduce the risk, to ensure that these things can find their way into the fleet in 2035 to 2050 timeframe. The public benefit would be across the board: less noise, fewer carbon emissions, and better local air quality around airports. We’re poised and ready for that and taking those technologies and integrating them together in the future.