Blog
Truck trailers in the U.S.: Leading from behind
So Tuesday was a really big deal for commercial trailers in the U.S. The U.S. Environment Protection Agency and the National Highway Traffic Safety Administration released the final rulemaking (FRM) for heavy-duty vehicle fuel-efficiency and greenhouse gas standards. By far the most significant new addition into the regulation are the trailers hauled by heavy-duty tractor trucks. OK, a little wonkish, agreed. But trailers were not included in the Phase 1 rule, and their inclusion in Phase 2 helped to squeeze an extra half a mile per gallon out of tractor-trailers. Ok, so what? Well, for the vehicles effected by the regulation, adding an extra 0.5 mpg across the entire tractor-trailer fleet in the U.S. translates to a reduction of about 7 billion gallons of diesel and 100 million metric tons of CO2. That’s roughly the same as taking all of the passenger cars and trucks in California off the road for an entire year! So including trailers in Phase 2 is indeed a big deal.
You’d expect us to be excited about this development, but what’s really encouraging is seeing all of the statements of support from heavy-duty vehicle and trailer manufacturers, as well as fleets. We’re still trying to wrap our heads around all of the various details of the regulatory program for trailers, but here are some of the key features.
Who’s regulated? In contrast to California’s regulation, under which individual trucking fleets are on the hook for installing acceptable trailer aerodynamic devices and low-rolling-resistance tires, the responsibility for complying with the federal rule falls squarely on trailer manufacturers. However, the agencies designed the certification process such that aerodynamic and tire testing responsibilities are shared by aero device and tire manufacturers so that the compliance process is not overly burdensome for trailer OEMs.
What kind of fuel-saving technology additions can we expect? As with the trucking sector, there is a tremendous diversity of trailer configurations and sizes to match all of the different types of goods that need to be hauled. To make sense of all of this complexity in a regulatory program, the agencies devised a grouping scheme that is simplified in the table below. As shown, box-type dry vans and refrigerated trailers of all sizes are required expected* to use combinations of aerodynamic, low rolling resistance (LRR) tire, and tire inflation pressure management technologies for compliance. Non-box trailers—which include a great variety of* trailer types such as flatbeds, tankers, grain trailers, auto transporters,* and container chassis—must install low rolling resistance tires and tire pressure management systems. There are exceptions and special provisions for both box and non-box trailers, but, in general, this is the way the rule is structured.
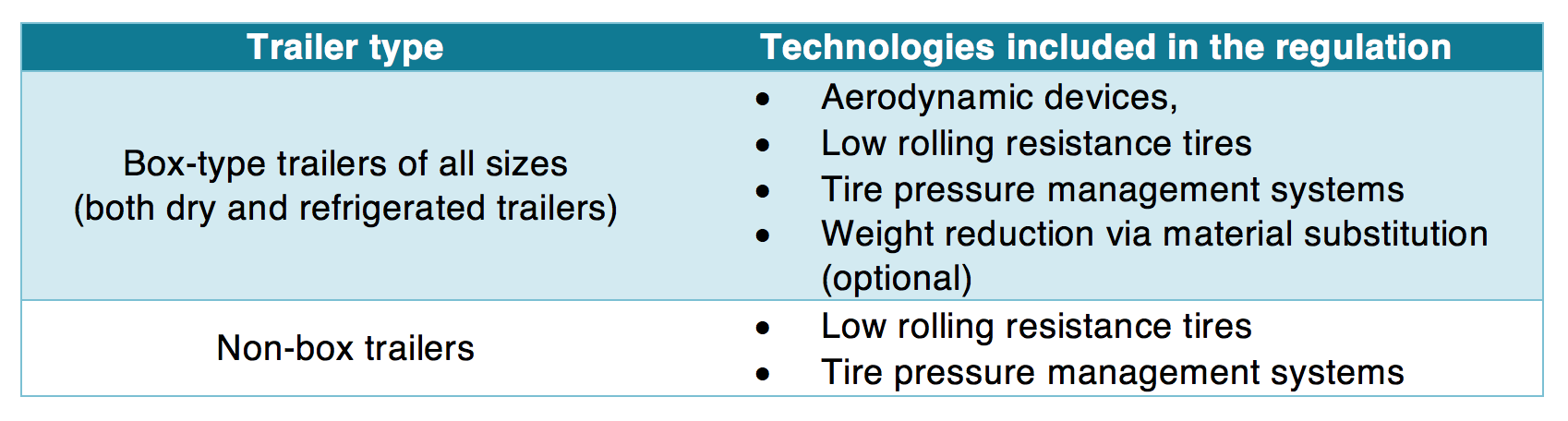
How does the regulation work? The rule is fairly straightforward for non-box trailer manufacturers, as these trailers simply have to follow a set schedule for using certain levels of LRR tires and also installing tire pressure systems. For box-type trailers, the requirements for aerodynamic technologies complicate things a bit. First, the trailer manufacturer has to figure out the aerodynamic performance of each of trailer models and configurations it plans to sell. Each trailer model is assigned into an aerodynamic bin based on how that trailer performs during aerodynamic testing. Some example technologies for each of the 7 aerodynamic bins are shown in the figure below. As you can see, increasing bin numbers imply increasing levels of aerodynamic sophistication. As shown in the far right column, each of the bins is assigned a default fuel consumption reduction percentage.
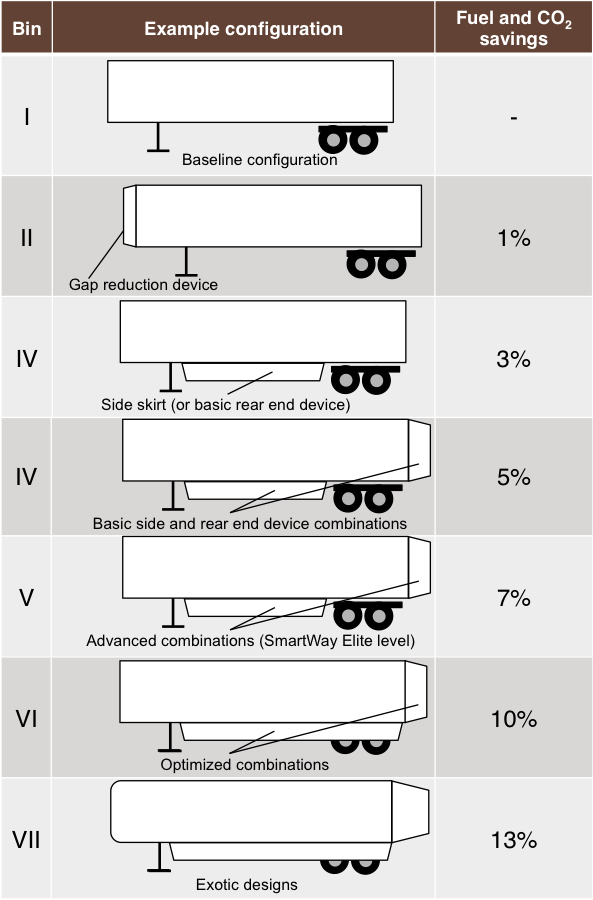
The figure below shows both the baseline distribution of bin numbers and the expected changes in adoption rates as a result of the regulation. This figure is for long dry van trailers, and you can see that over time, there will be increasing numbers of the highly efficient Bin V and VI trailers that must use combinations of side skirts and rear end devices to achieve compliance.
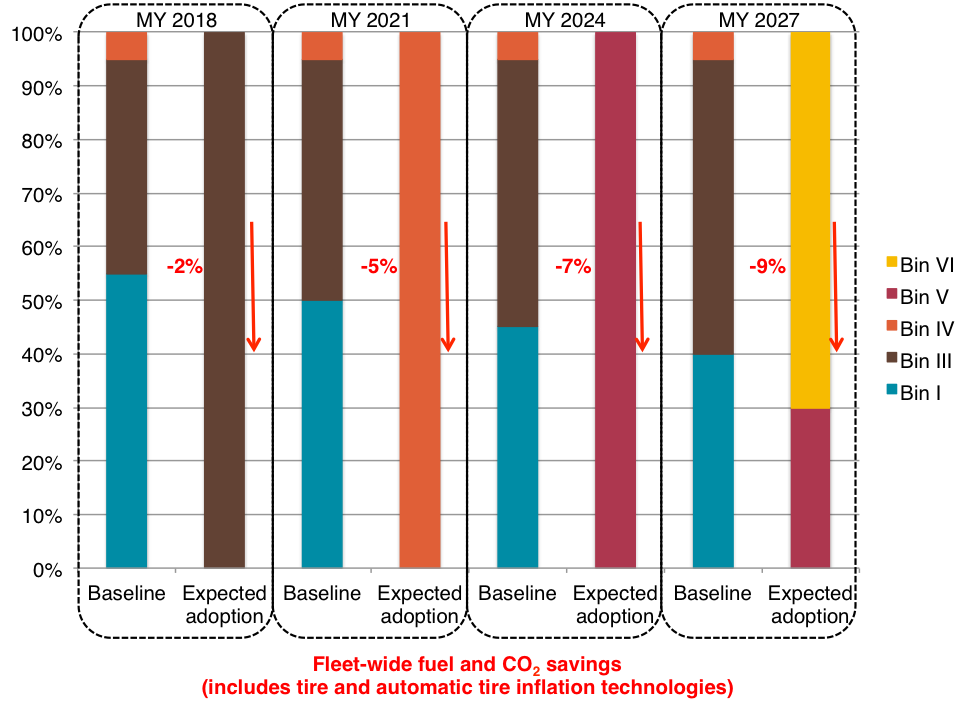
What do the costs look like? Across the fleet, additional technology costs range from roughly $200 to $1,400, depending on the type of trailer. The large majority of these trailer technology investments are expected to payback within a year. Our research in the U.S. and Canada has shown that the cost of trailer fuel-saving technologies has dropped considerably in the past 5-7 years. This has made the economics quite attractive for a number of fleets, even in the absence of regulation, as we’ve seen uptake of these technologies continue to accelerate in recent years.
With the Phase 2 regulation, trailers in the U.S. become the first in the world to be regulated based on their impact on fuel efficiency and carbon emissions. The rule ensures the accelerated adoption of proven cost-effective efficiency technologies for trailers and also encourages continued innovation in tires, aerodynamics, and weight reduction. While trailers are behind the tractors in a literal sense, they have also historically lagged behind trucks in terms of focus on efficiency technologies. Well, the newly released Phase 2 regulation signals a changing of the guard. Trailers in the U.S. will be leading the world on getting fuel-saving technologies on the road that are a major boon to trucking fleets and society as a whole.
* The original text was corrected and updated on 9/9/2016 to appropriately reflect the ruling