Blog
Pioneering zero-emission off-road machinery: Inside Oslo’s Fornebu Line project
The Fornebu Line project in Oslo, Norway is a transformative metro extension designed to meet growing transportation needs while aligning with the city’s ambitious climate goals. By integrating zero-emission off-road machinery and innovative strategies, the project offers valuable insights for off-road decarbonization efforts around the world.
I was lucky enough to visit Fornebu Line while in Oslo for the Off-Road Decarbonization Symposium 2024 co-hosted by the ICCT, the City of Oslo, and C40 Cities. This nearly 8 km metro extension includes six new stations and is managed by a dedicated agency within Oslo Municipality; it was designed by COWI A/S and Multiconsult ASA and aims to reduce surface congestion, accommodate future traffic growth, and support urban expansion. Construction began in 2020, and completion is expected in 2029. This project is also contributing to Oslo’s broader goals of zero emissions for all municipal construction projects by 2025 and for all construction work by 2030.
Strategy for zero-emission machinery
In procurement decisions for Fornebu, sustainability is weighted 20%, price 40%, and quality 40%. While biogas-powered machinery has been a transitional fuel in Oslo’s push for “greener” construction, it’s not being used in this project because of concerns about its safety in confined environments like tunnels. Instead, electric off-road machinery, a zero-emission solution, is being used for complex tasks such as ground preparation and demolition.
At the site of K1B Madserud, one of Fornebu’s sub-projects, the Volvo L25 electric compact wheel loader, which has a 5-ton operating weight and high agility, is used for material transport, surface preparation, and waste management. Its 40 kWh lithium-ion battery provides up to 8 hours of operation on a single charge. Alongside it, a 20-ton LiuGong electric wheel loader handles heavier tasks like moving large volumes of soil and loading materials. Together, these showcase how zero-emission equipment of different sizes and power can complement each other.
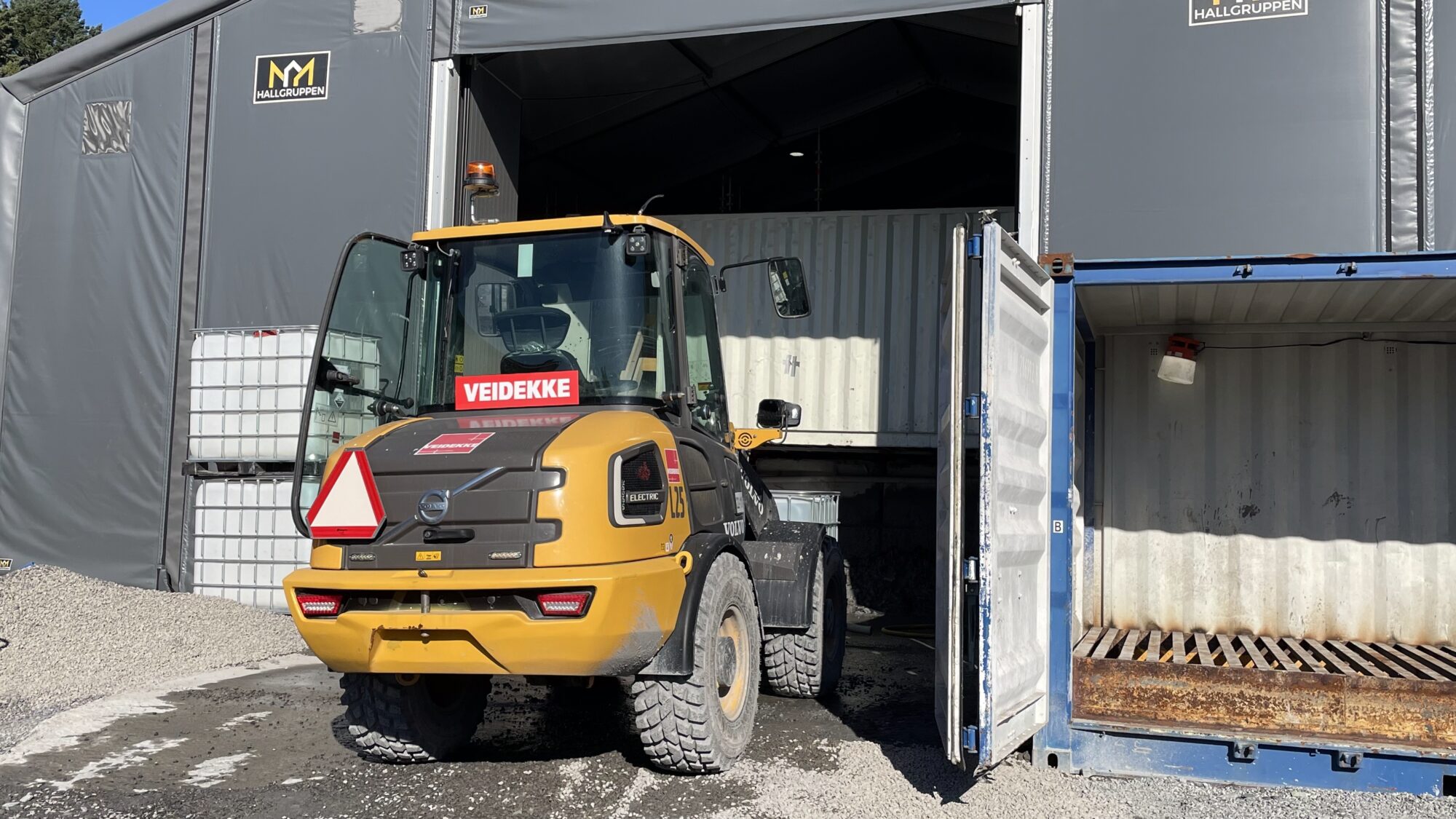
A Volvo L25 electric compact wheel loader at the K1B Madserud site. Photo by Jinjian Li.
Two SANY SKT90E electric trucks produced in China and powered by high-capacity lithium batteries handle on- and off-site material transport. These 60-ton mining trucks have a total power output of 740 kW and productivity-enhancing features such as GPS modules and intelligent self-diagnosis systems.
An ANEO mobile power container is one of the on-site fast-charging solutions for electric machinery that we observed during the site visit. It’s equipped with high-capacity batteries to ensure a flexible and efficient energy supply and minimize disruptions to construction work.
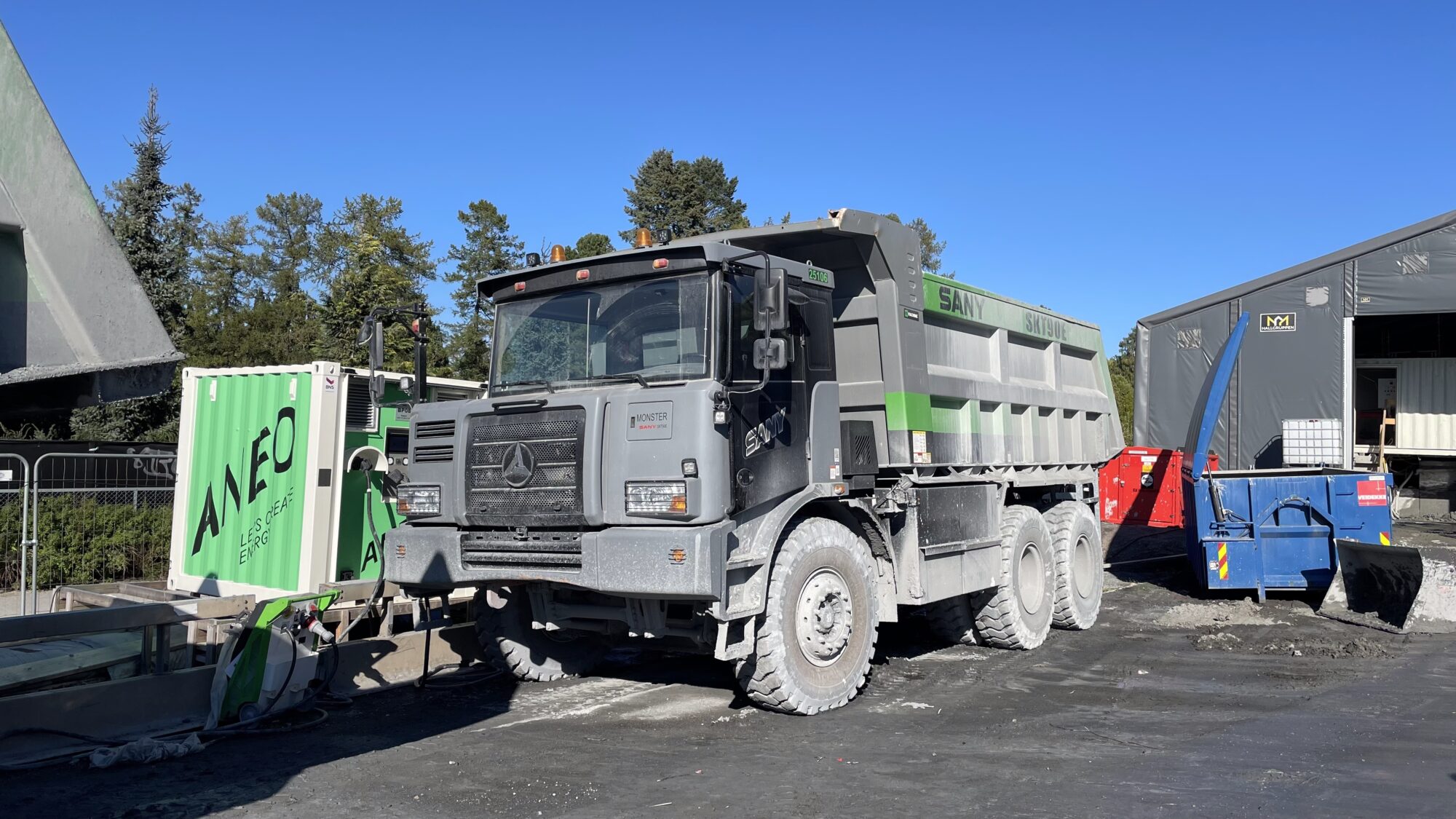
A SANY SKT90E electric off-highway mining truck and an ANEO power container at the K1B Madserud site. Photo by Jinjian Li.
Environmental, social, and cost benefits
Construction emissions are approximately 17% of the Fornebu project’s carbon footprint, and material production dominates with around 66% of emissions. At the time of the September 2024 visit, the project had achieved 61% zero-emission machinery use across all six sub-projects not directly tied to the new stations, with the K1B sub-project surpassing 75%.
Beyond environmental gains, electric machines produce significantly less noise than their diesel counterparts, feature ergonomic cabin designs, and have the potential for automation that can improve working conditions for operators. According to site managers involved in the K1B Madserud sub-project, the electric machinery is proving to be versatile and capable of handling various tasks such as fully loaded uphill operations, all while requiring minimal maintenance.
While the upfront cost of electric machinery remains a challenge—rental prices for electric wheel loaders, for instance, are two-to-three times higher than comparable diesel models—their cost is a relatively small part of the metro project’s total budget. Additionally, in areas of Europe with high diesel prices, unpublished analyses have shown that using electric small excavators and wheel loaders can cut energy costs by approximately half. Declining battery costs are expected to improve the economic outlook even further, and the market’s positive response to pilot demonstrations is driving affordability. Norway’s planned rollout of around 9,000 projects adopting zero-emission machinery has spurred demand for specialized electric equipment and is incentivizing manufacturers to scale production. The resulting mass manufacturing and standardization of designs is expected to narrow the cost gap with conventional machinery.
Lessons for others
One key learning from the Fornebu Line project is the pivotal role of local governments. Here Oslo set the stage with its climate goals and the zero-emission machinery targets in its procurement policies for municipal projects. We see that procurement can be a powerful tool for driving the transition.
Additionally, the importance of charging infrastructure cannot be overstated. Transitioning to electric construction machinery increases power demand, particularly during peak charging times on work shifts, and demand can exceed 500 kW. Given this, measures such as optimizing charging schedules, deploying charging containers (as demonstrated by the Fornebu project), and installing grid or network stations are often needed to help manage energy demands. Furthermore, ensuring a reliable supply of high-voltage power requires close coordination between project developers, construction contractors, and grid companies throughout the planning and implementation phases.
Finally, early and strategic planning is essential. There was a lengthy procurement process for the Fornebu Line project due to challenges in securing specialized electric machinery, especially some of the large models. There was not only an issue of limited global availability, but these models also require customized components such as vibration-resistant batteries. This was compounded by supply chain disruptions during the COVID-19 pandemic. Additionally, coordinating high-voltage grid capacity for peak-charging demands required meticulous planning, including mapping machinery energy needs, calculating peak loads, and getting grid approvals. This multi-stakeholder process can take months. Streamlining processes from the outset and strategic planning can save time and improve the efficiency of adopting zero-emission machinery.
Acknowledgement: The author extends sincere gratitude to the City of Oslo for coordinating the site visit to the Fornebu Line project and to both the City of Oslo and C40 Cities for sharing valuable insights on Norway’s charging infrastructure for zero-emission applications.
Author
Related Publications
Incentivizing zero-emission off-road machinery
The global market for off-road mobile equipment, including agricultural, construction, and mining machinery, has surged in the last two decades.